Health and safety Coordinator
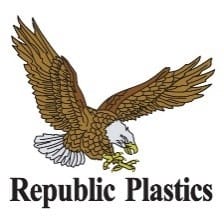
Website Republic Plastics
Job Details
Description
Responsibilities:
To perform this job successfully, this individual must be able to perform each job duty satisfactorily.
The requirements listed below are representative of the knowledge, skill, and/or ability required.
Reasonable accommodations may be made to enable individuals with disabilities to perform the
essential functions. This opportunity requires approximately 25% travel to our locations in Texas, Arizona and Tennessee. The Health and Safety Coordinator’s essential job duties include, but are not limited
to the following:
Follow safety and sanitation rules and regulations.
Creates and manages safety training schedule for all associates, including safety
training new associates and ongoing training for existing associates.
Works with plant management to ensure that all associates receive required safety
training.
Coordinates and ensures proper documentation of safety training for associates.
Evaluates and manages existing safety programs and recommends changes and
additional safety programs as needed.
Measures, evaluates and manages hazard control systems, policies and procedures.
Develops controls for identified hazards and coordinates implementation of controls
from results of hazard analysis.
Coordinate and conduct periodic on-site safety walk through inspections. Identifies
and evaluates hazardous conditions and practices in the workplace.
Provides advice and counseling to plant and senior management on all safety
compliance regulations and requirements.
Coordinates and ensures proper investigation and documentation of employee
injuries, workplace accidents, near misses, and all other safety related incidents.
Identifies and evaluates safety trends such as incident rate, number of incidents,
number of lost time incidents, injury types, incident severity, etc.
Responsible for overall administration of workers compensation and return to work
programs.
Works with other team members to complete tasks and achieve department goals.
Follow instructions and directions provided by the Director of Human Resources &
Legal Affairs and/or other members of corporate management.
Follow, comply with and model all company rules, policies and directives, including
the Associate Handbook
Attends work as scheduled, including 40 or more hours per week and weekends and
evenings as required. Must also be able to also effectively respond to issues related to a
24-hour/7 days a week operation.
All other tasks and duties as assigned.
This list of job duties is not all-encompassing. The Health & Safety Coordinator will be expected to
perform all other duties that will be assigned as necessary.
Required Physical and Mental Abilities
The physical and mental abilities described here are representative of those that must be met by an
associate to successfully perform the essential functions of the Health and Safety Coordinator position.
Reasonable accommodations may be made to enable individuals with disabilities to perform the
essential functions.
General Physical Requirements – The ability to stand, walk, hear, and smell. The
ability to use hands to finger, handle, or feel and reach with hands and arms. The
associate is occasionally required to sit, climb or balance; and stoop, kneel, crouch
or crawl.
Active Listening – Giving full attention to what other people are saying, taking time
to understand the points being made, asking questions as appropriate, and not
interrupting at inappropriate times.
Coordination – Adjusting actions in relation to others’ actions.
Speaking – Talking to others to convey information effectively.
Learning Strategies – Selecting and using training/instructional methods and
procedures appropriate for the situation when learning or teaching new things.
Monitoring – Monitoring/Assessing performance of yourself, other individuals, or
organizations to make improvements or take corrective action.
Monitoring – Monitoring/Assessing performance of yourself, other individuals, or
organizations to make improvements or take corrective action.
Instructing – Teaching others how to do something.
Positive Attitude – A mental attitude that interprets situations and events as being
best or optimized.
Time Management – Managing one’s own time and the time of others. Must have
the ability to manage multiple, competing priorities and projects.
Reading Comprehension – Understanding written sentences and paragraphs in work
related documents.
Social Perceptiveness – Being aware of others’ reactions and understanding why
they react as they do.
Lifting – The ability to occasionally lift and or move up to 10 pounds, frequently lift
and or move up to 25 pounds, and occasionally lift and or move up to 50 pounds.
Vision and Hearing – Specific vision abilities required by this job include close vision,
distance vision, color vision, peripheral vision, depth perception, and ability to
adjust focus. In addition, good hearing is required.
Manual Dexterity – The ability to quickly move your hand, your hand together with
your arm or your two hands to grasp, manipulate, or assemble objects.
Multi-limb Coordination – The ability to coordinate two or more limbs (for example,
two arms, two legs, or one arm and one leg) while sitting, standing, or lying down.
It does not involve performing the activities while the whole body is in motion.
Supervisory Responsibilities
Works in a team environment led and directed by the Director of Human Resources & Legal Affairs
and/or other members of corporate management.
Required Education, Experience, and other Qualifications:
A Bachelor’s Degree in a related field plus 5-7 years of experience coordinating and/or managing
health and safety compliance a manufacturing environment or a minimum of 10+ years of experience
coordinating and/or managing health and safety compliance a manufacturing environment, including,
but not limited to, experience with Project Safety Management, supervising and managing employees,
department budgeting and finances, and departmental operations.
Experience in Plastics Thermoforming is preferred.
Other required qualifications:
High level of technical expertise and the ability to apply skills to continuous process
improvement while maintaining maximum level of safety
OSHA 30 hour certification preferred
Demonstrated leadership skills and abilities
Excellent communication skills up and down organizational structure
Strong planning, organizational and follow up skills
Excellent people and process management skills
Computer Skills: Must possess intermediate level computer knowledge, including, but not
limited to, the ability to generate and edit word processing documents and spreadsheet reports.
Language Skills: The ability to draft, read and comprehend high level correspondence in English as
well as communicate orally and in writing in English at a collegiate level. The ability to effectively
present information in one on one and group situations to customers, vendors and Associates of The
Company.
Mathematical Skills: The ability to apply concepts such as fractions, percentages, ratios, and
proportions to practical situations.
Reasoning Ability: Ability to define problems, collect data, establish facts, and draw valid
conclusions. Ability to provide legal reasoning and analysis in a wide range of business contexts.
Work Environment: The work environment characteristics described here are representative of
those an Associate encounters while performing the essential functions of this job. Reasonable
accommodations may be made to enable individuals with disabilities to perform the essential
functions. While performing the duties of this job, the Associate is regularly exposed to long periods
of sitting and working in front of a computer in an office setting. Frequently the Associate will be
exposed when out on the production floor to moving mechanical parts, high, precarious places;
fumes or airborne particles; risk of electrical shock; and vibration. The noise level in the regular
work environment is usually low to moderate. The Associate may also be exposed while on the
production floor to high-pressure operating systems, including water, air, molten plastics and
butane. The Associate will be exposed to temperatures and atmospheric conditions typical of a nonclimate
controlled manufacturing facility environment, including excessively warm or cold
temperatures.
Comments: This is not an all-encompassing list, and other duties will be assigned as required. This
position is a key position in the self-directed – teamwork driven production environment of Republic Plastics. An individual in the Administrative Supervisor position will have to be dedicated,
responsible, highly motivated, safety and quality conscious.
Company Core Values
All Associates within our manufacturing organization, in adherence to our corporate values, will treat
each other and anyone who enters our facility with the utmost respect and dignity. We will endeavor
to excel at, and hold each other to the following values in everything we do.
Safety – a commitment from each of us to follow rules and guidelines to ensure
freedom from the occurrence or risk of injury, danger, or loss.
Teamwork – each of us doing our part to support the overall goal, which is to
increase the profitability of the company and its associates.
Accountability – the willingness to accept responsibility for one’s actions.
Positive Attitude – a state of mind in relationship to our work environment and
accomplishing our goals.
Quality/Excellence – the nature by which each of our products, service and
interaction can be identified as good or worthy.
Integrity/Honesty – adhering to a high set of ethical standards, the unimpaired
state of continual improvement personally and professionally.
Commitment – pledging oneself to the cause or goal